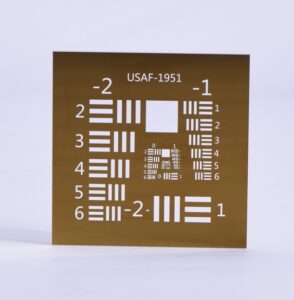
Judging from the current market conditions, machine vision, an automated imaging technology, has been widely used, and its application advantages in industrial production, intelligent transportation, security monitoring and other fields have been recognized by the majority of users. The machine vision system includes two major links: image acquisition and image processing. It is composed of core components such as light sources, lenses, industrial cameras, and image processing software. It mainly has three major functions: positioning, identification, and detection. In the entire machine vision system imaging process, high-precision system calibration is the foundation and focus of achieving high-definition imaging, and it should have a direct impact on the final result.
Classification of machine vision calibration
The relationship between the three-dimensional geometric position of a certain point on the surface of a space object and its corresponding point in the image is determined by the geometric model of industrial camera imaging. These geometric model parameters are industrial camera parameters. Under normal circumstances, these parameters must be obtained through experiments and calculations, and this experiment and calculation process is called machine vision system calibration. at present
Machine vision calibration mainly includes two categories: traditional calibration methods and self-calibration methods:
One is the traditional machine vision calibration method. The traditional machine vision calibration method requires a calibration reference object. Under a certain industrial camera model, the internal parameters and external parameters of the camera model can be obtained by performing image processing on the specific calibration reference object and using a series of mathematical transformation formulas to calculate and optimize. In addition, in order to improve calculation accuracy, nonlinear distortion correction parameters need to be determined. According to the differences in calibration reference objects and algorithm ideas, traditional machine vision calibration methods can be divided into camera calibration based on 3D stereoscopic targets and camera calibration based on 2D planar targets. However, it should be noted that this calibration method does not work well when the scene is unknown or the camera moves arbitrarily, and it is even difficult to achieve.
Second, machine vision self-calibration method.
The machine vision self-calibration method was first proposed by Faugeras, Luong, Maybank and others in the early 1990s. This self-calibration method uses the constraint relationship between the parameters of the industrial camera itself for calibration, and it is not related to the scene or Industrial cameras have nothing to do with motion, so they are more flexible than traditional calibration methods.
The role of machine vision calibration
The accuracy of machine vision calibration directly affects the accuracy of system imaging. It can be said that only by doing a good job in the early calibration work can subsequent work proceed normally. Therefore, improving calibration accuracy is one of the important aspects of current scientific research work. The existence of machine vision system calibration methods, especially self-calibration methods, has greatly improved imaging accuracy. Next, researchers will continue to optimize and upgrade calibration methods, such as further research on how to improve the robustness of calibration algorithms, etc. .
Through the above introduction, we understand the importance of machine vision system calibration in the entire machine vision imaging process, which directly affects the clarity and accuracy of the final image obtained. The calibration method based on the machine vision system has certain performance advantages over manual calibration or other calibration methods. At present, calibration plates are usually used for machine vision system calibration. The use of calibration plates can greatly improve detection and measurement accuracy indicators, effectively ensuring that machine vision system calibration can fully play its role in precision measurement and inspection applications.
We know that when the camera is calibrated, it first needs to establish a geometric model of the camera imaging. By photographing a flat plate with a fixed spacing pattern array and calculating it through the calibration algorithm, the geometric model of the camera can finally be obtained, thereby obtaining high-precision measurements. and reconstruction results. In this calibration process, the flat plate with a fixed spacing pattern array used is the calibration plate we are going to discuss today.
The role of the calibration board in machine vision system calibration mainly has the following two aspects:
1. Correct deformity. When using machine vision technology for precision measurement or inspection, the distortion of the lens itself is inevitable. Using a calibration plate can correct lens distortion and effectively ensure imaging accuracy in applications such as machine vision, image measurement, and three-dimensional reconstruction. .
2. Determine the relationship. The calibration plate can be used to determine the conversion relationship between physical dimensions and pixels, and to determine the relationship between the three-dimensional geometric position of a point on the surface of a space object and its corresponding point in the image, making the resulting image more accurate.
To meet the accuracy requirements, a high level of software technology support is required, as well as more realistic and accurate image information. Judging from the role of the calibration board in the calibration of the machine vision system, it is indeed effective in ensuring imaging precision and accuracy. has very important significance.
OSTHK can provide customized high-precision calibration plates and provide accurate hardware guarantee during the calibration process. Welcome to contact us, we can provide professional and comprehensive services.